Unique battery reuse, repair and recycling plant opened in Germany
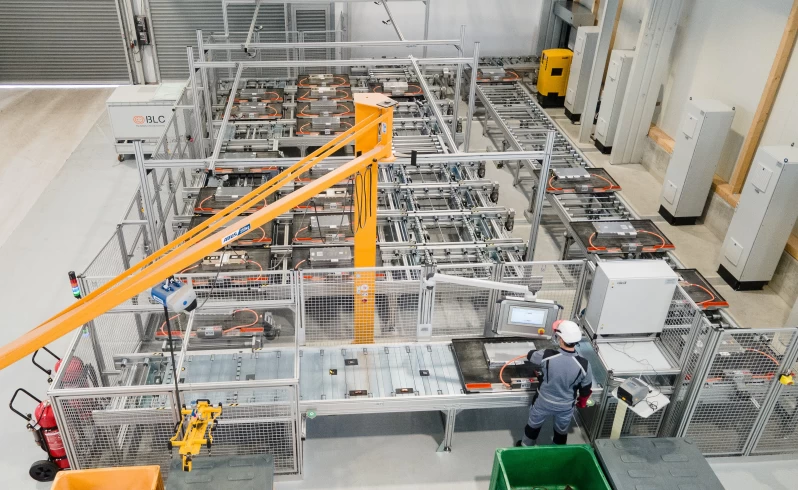
The BLC battery deep discharge facility, which just opened in Magdeburg, is now one of the largest in Europe for dismantling batteries before they are reused or recycled. BLC is a joint venture between Remondis subsidiary TSR Automotive and Rhenus Automotive.
According to industry estimates, just 10% of all automotive batteries are sufficient to power the world’s stationary storage needs. For automotive batteries to be reused in stationary storage, where their lifecycle is extended by another 10 years, they must be tested and dismantled.
Processes used for preparation for a second life or shredding for recycling have so far been labor-intensive. The newly opened BLC plant in Magdeburg is the first to use a highly automated process for this purpose.
The automated process used by BLC in Magdeburg shortens the deep discharging of high-performance batteries that previously took up to 24 hours to less than 15 minutes. Bosch Rexroth is supplying BLC with one of the first automated systems for discharging in Europe.
“The automated discharge developed by Bosch Rexroth not only simplifies recycling, it also increases efficiency and safety. Modules can be deep discharged within a few minutes. This is an enormous gain in productivity. Risks such as short circuits and fires are minimized,” explained Lukas Brandl, Managing Director at BLC.
The company says its new center in the port of Magdeburg will be able to process up to 15,000 metric tons of batteries per annum, which is about six times more than the company’s other plant in Rheda-Wiedenbrück.
In Magdeburg, dismantling work will be undertaken with the support of robots. “Electric batteries weigh as much as 700 kilograms and have about 180 screws. Dismantling them is associated with considerable effort. If the employees here have to handle each screw manually, this is detrimental to their health, motivation and process efficiency. We want to prevent that,” says Florian Karlstedt, a member of the management team at BLC.
As robots take over the more hazardous work quickly and safely, human staff can concentrate on tasks like quality controls, cable connections or data analysis. “This high level of automation hasn’t been common in the sector up to now, as the processes are very complex and very sophisticated,” Florian Karlstedt continues.
The company says making tested modules available for second-life solutions such as stationary storage systems (BESS) is already a significant part of its activities. The proximity to automotive companies is a primary benefit of the plant’s location with the easy and short transportation of batteries. “We want to be where our customers are in order to create logistical operations that are as efficient as possible.” Lukas Brandl, also a member of management, explains.
Creating value through effective and efficient processes and supply chains to maximize the use of valuable battery resources is fast becoming a unique German proficiency. Thanks to its close connections with Rhenus Automotive and TSR Automotive, BLC says it can build on the expert knowledge available in logistics, assembly, handling waste and raw materials, and battery handling.
This article was corrected on September 4, 2024, after BLC kindly further clarified the described processes. The corrections reflect that the unique system is the automated deep discharge system for batteries, and that batteries destined for a second life are tested at the Magdeburg facility, but do not go through a deep discharge, whereas those destined for recycling do.