Solid-state batteries enter pilot production, costs expected to drastically drop
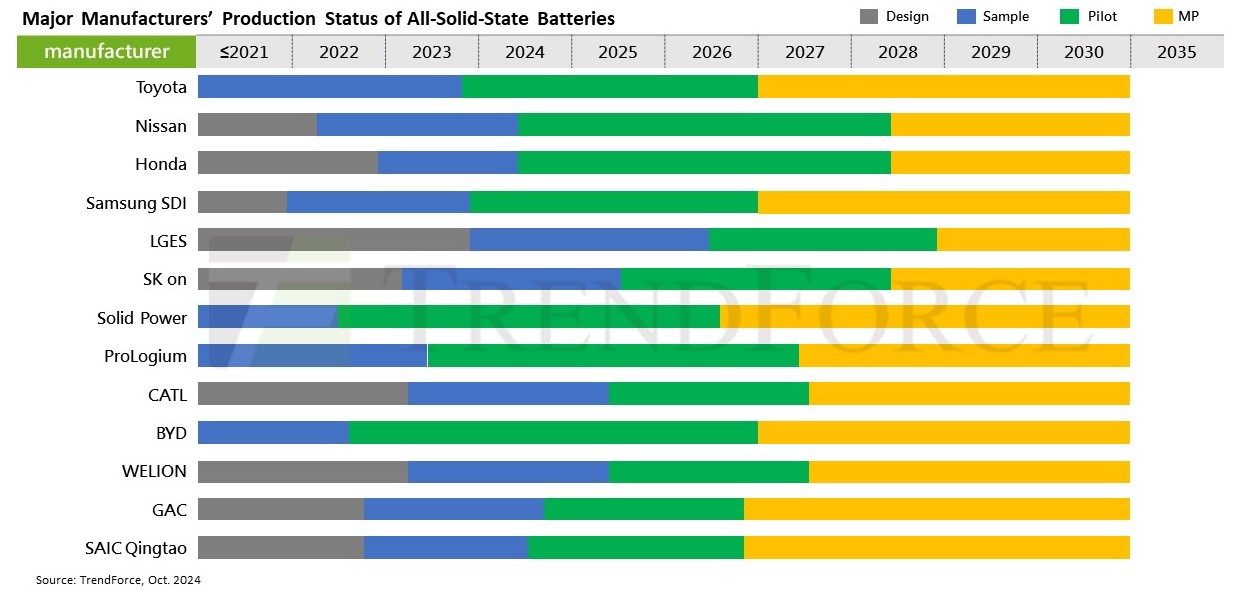
The push to commercialize solid-state batteries (SSBs) is underway with industries from automotive to storage betting on the technology. But while the hype around full solid-state batteries has somewhat subsided, with the technology taking longer than expected to take off, semi-solid-state batteries, which use a hybrid design of solid and liquid electrolyte, have been making steady progress toward commercialization.
TrendForce’s latest findings reveal that major manufacturers across the globe – such as Toyota, Nissan, and Samsung SDI – have already begun pilot production of all-solid-state batteries. It is estimated that production volumes could have GWh levels by 2027 as these companies race to scale up production.
The decades-old technology promises improvements in safety and energy density, but has so far struggled to achieve commercial success. High production costs, complex manufacturing processes, and a lack of a mature supply chain have held back deployment.
In the meantime, semi-solid-state batteries have already been commercialized to a good extent and are currently deployed in electric vehicles. According to TrendForce, they have already reached GWh-level scale installation, with cell energy densities ranging from 300–360 Wh/kg.
The initial price of semi-solid-state cells exceeds CNY 1/Wh ($0,14/Wh) due to small production scales and the relative immaturity of manufacturing technologies. TrendForce anticipates that with increased production scale and technological advancements, the comprehensive cost of semi-solid-state batteries could drop below CNY 0.4/Wh by 2035.
All-solid-state batteries are moving from prototype sample cells to engineering-scale production and are also expected to encounter high early-stage production costs that could raise initial product prices. TrendForce projects that, by 2030, if the scale of all-solid-state battery applications surpasses 10 GWh, cell prices will likely fall to around CNY 1/Wh. By 2035, cell prices could decline further to CNY 0.6–0.7/Wh with rapid, large-scale market expansion.
Focus on sulfide-based SSB technology
Today, there are three competing ways to do solid-state batteries based on different types of electrolyte, and each has its own set of technological bottlenecks. Polymer-based solid-state batteries are relatively mature and have already been commercialized in parts of Europe. For instance, French company Blue Solutions already produces such solid-state batteries for Daimler electric buses. However, this class of batteries still faces challenges in terms of voltage tolerance and ionic conductivity.
Oxide solid-state electrolytes are known as the most chemically stable class of solid-state batteries but are difficult to manufacture. The “solid-solid” contact between the electrolyte and the cathode/anode active materials leads to higher internal resistance.
Sulfide-based solid-state batteries show particularly strong potential due to their ionic conductivity, which is closest to, and may even exceed, that of liquid electrolytes. This class of solid-state batteries is explored by major developers, including Toyota, Samsung SDI, LGES, SK On, CATL, and BYD. However, this chemistry is unstable in air and highly sensitive to moisture, adding complexity to the production process and potentially releasing H2S gas, which is poisonous as well as flammable.
TrendForce’s view on the development of solid-state battery technology is cautious yet optimistic. “Although key performance indicators such as charge-discharge rates and cycle life have not yet reached commercialization standards—and current costs remain uncompetitive with liquid li-ion batteries—SSB costs will improve significantly as production scales up, owing to strong government policies and capital investment,” the analysts say.